Cold rolled stainless steel band is increasingly becoming a vital component in various industries due to its superior characteristics and versatile applications. When considering purchasing or working with this advanced material, understanding the intricacies of its manufacturing process, properties, and benefits is key to leveraging its full potential.
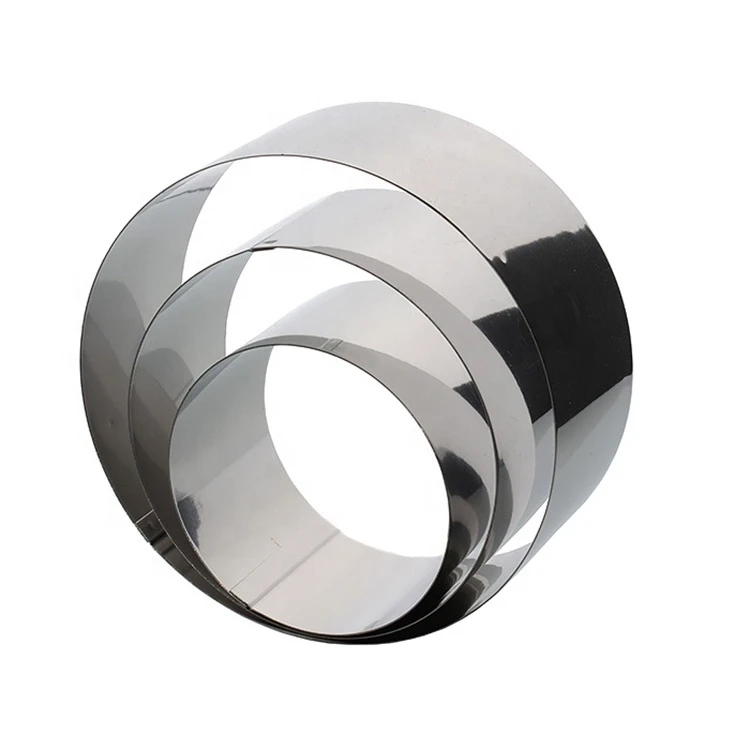
Cold rolling involves passing stainless steel through a series of rollers at a temperature below its recrystallization point, which is typically at room temperature. This process helps produce a material with a smoother surface finish, closer dimensional tolerances, and a refined grain structure. These characteristics are crucial for industries that demand high-precision components, such as automotive, aerospace, and construction.
From an experience standpoint, those who have worked closely with cold rolled stainless steel band often highlight the material's impressive strength-to-weight ratio. This property not only facilitates ease of handling and transport but also allows for its use in applications where weight is a critical factor. For example, in the automotive industry, reducing vehicle weight is paramount for fuel efficiency and performance, and the use of cold rolled stainless steel band can contribute significantly to achieving these objectives.
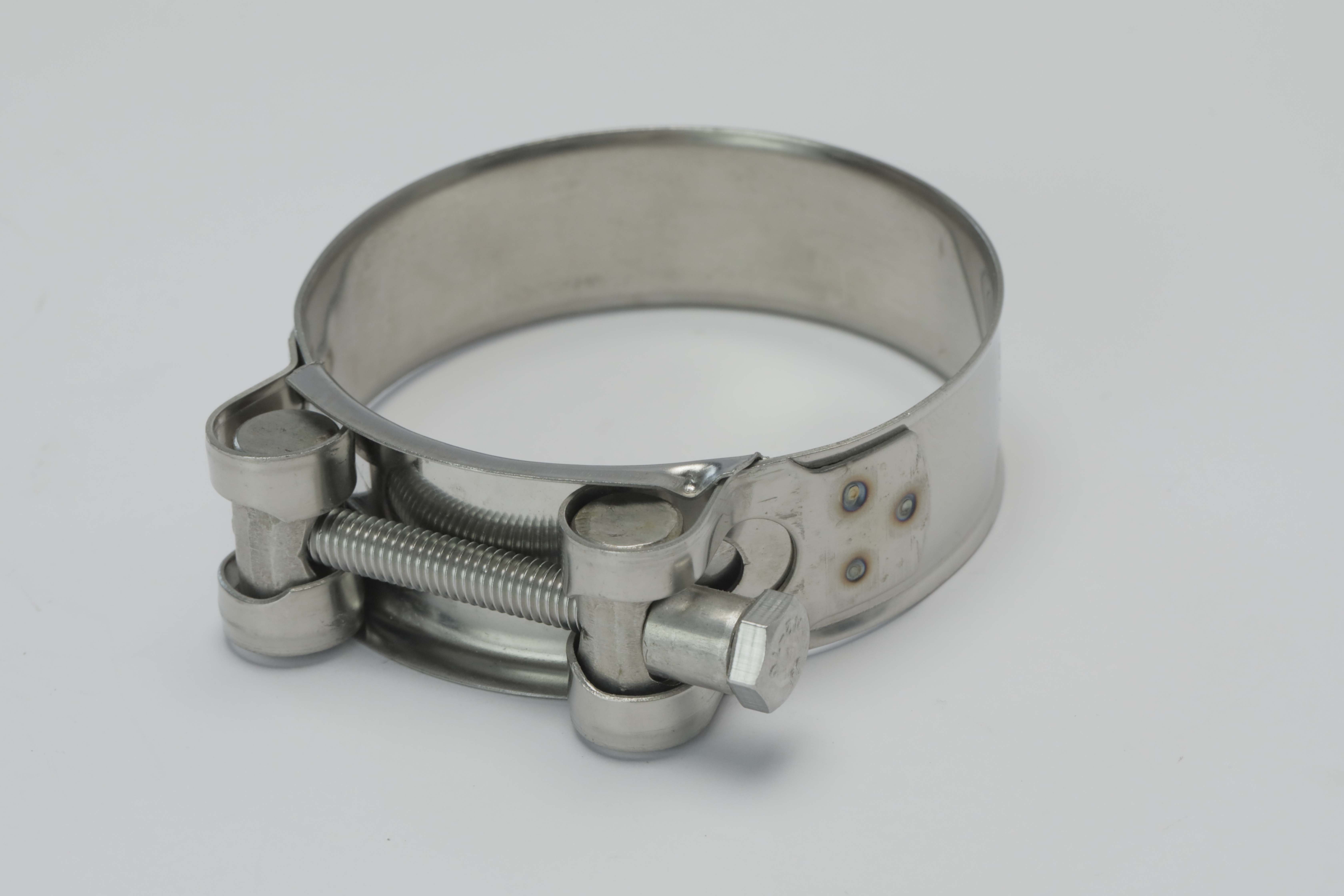
Professionals in the field consistently emphasize the importance of the material’s corrosion resistance, which is enhanced through the cold rolling process. This makes it an excellent choice for environments exposed to harsh weather conditions or corrosive chemicals. For instance, architects and engineers might choose cold rolled stainless steel for structural components in coastal buildings to ensure longevity and reduced maintenance costs over time.
cold rolled stainless steel band
Expertise in metallurgy and materials science reveals that the mechanical properties of cold rolled stainless steel band, such as tensile strength and hardness, are substantially improved compared to their hot rolled counterparts. This improvement is due to the work hardening that occurs during cold rolling, which aligns and deforms the metal's crystal structures, granting it superior resilience under stress. Thus, for applications that demand high durability and reliability, such as in manufacturing equipment or heavy machinery, this material is often the favored option.
A key aspect of authoritativeness when discussing cold rolled stainless steel band is understanding industry standards and certifications. Products like these are subject to stringent quality controls and are often certified according to international standards, such as ISO 9001 or ASTM. Such certifications ensure that the material meets rigorous quality specifications, providing buyers and end-users with confidence in its performance across various applications.
Trustworthiness in the selection and use of cold rolled stainless steel band also hinges on choosing reputable suppliers. Many reputable companies maintain traceability of their materials, offering documentation that verifies the source and quality of the stainless steel. This guarantees that the end product not only meets industry requirements but also aligns with project-specific needs, enhancing overall trust in the product's efficacy.
In conclusion, cold rolled stainless steel band stands out as an essential material for a diverse range of high-precision and durability-demanding applications. By leveraging expert knowledge, understanding industry standards, and choosing a trustworthy supplier, businesses can maximize the benefits of this versatile material. Whether in architecture, automotive, or industrial manufacturing, cold rolled stainless steel band offers unmatched quality that translates into long-term performance and reliability.