When selecting the right 150mm hose clamp for your project, understanding the essentials across various criteria can significantly enhance your project’s success. With over a decade of experience in the field of industrial fittings and more installations than one could count, this guide provides expert insights into 150mm hose clamps—a crucial yet often overlooked component in many mechanical systems.
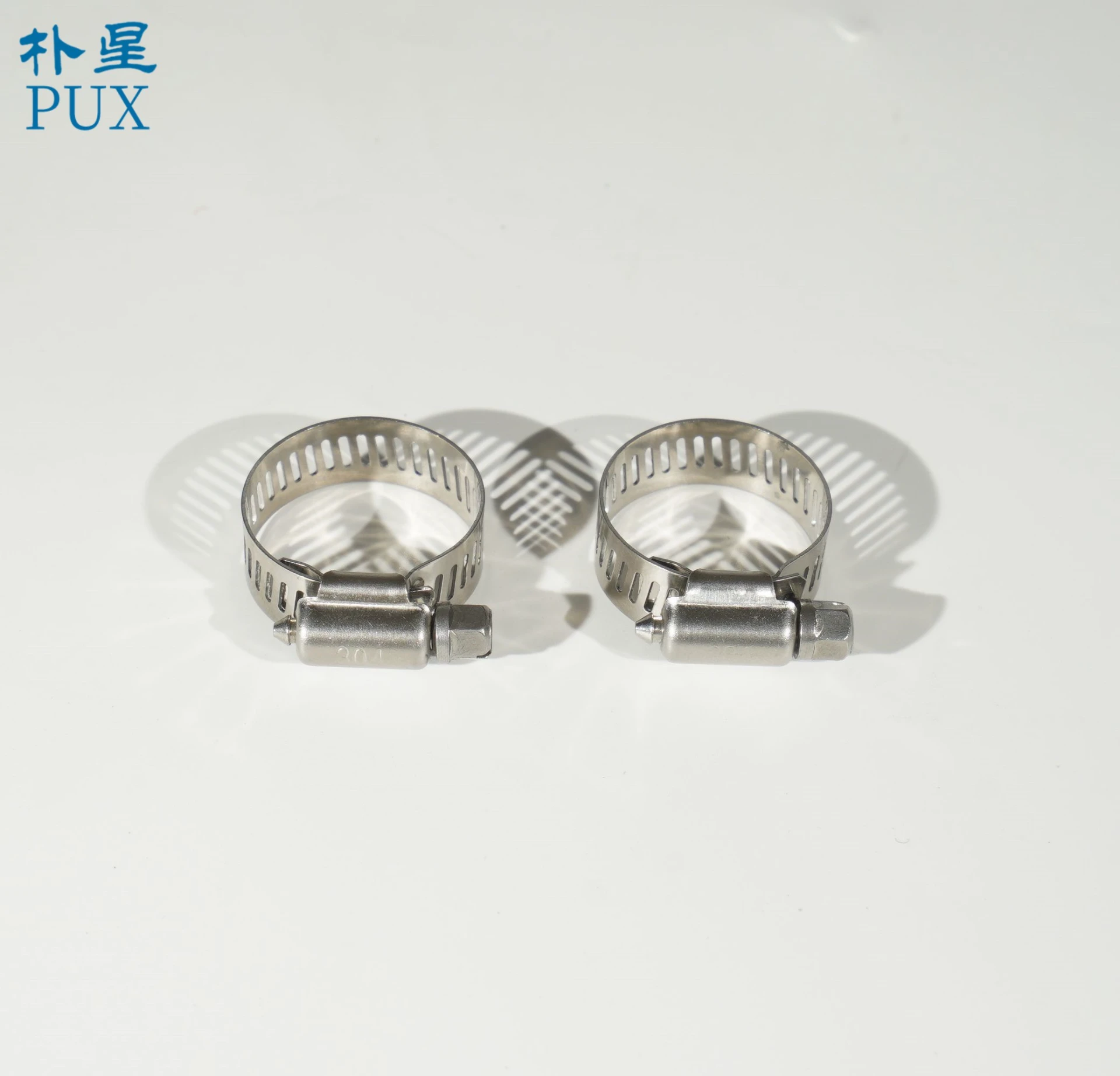
Material Selection Matters
Choosing the right material for your hose clamp is pivotal. Stainless steel is the gold standard in hose clamp materials due to its durability and resistance to corrosion. It is particularly beneficial in environments exposed to moisture or chemicals. For projects where budget constraints exist but durability is not to be compromised, a combination of stainless steel with a zinc-plated screw can still deliver satisfactory performance. Nylon or plastic clamps might be cost-effective for lighter applications but can deteriorate over time, especially in high-temperature contexts.
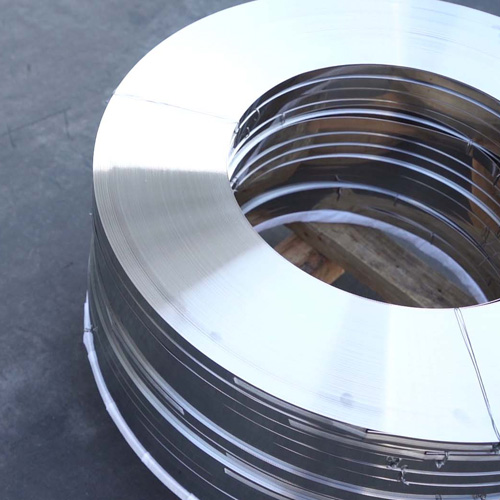
Design Considerations
Clamps are not one-size-fits-all; the design intricacies matter. The worm-drive design, which is prevalent in 150mm hose clamps, offers ease of adjustment coupled with reliable sealing capability. This type of clamp uses a screw to tighten the band around the hose, making it versatile and adjustable—a necessary feature when precision is paramount. Contrast this with T-bolt designs, which provide a more uniform sealing pressure and are immensely effective for high-pressure applications. Each design caters to different pressure levels, and understanding this mechanic can prevent future system failures.
Installation Techniques
Proper installation minimizes risks and maximizes efficiency. A common oversight during installation is over-tightening, which can damage the host material or create an imperfect seal. A precise balance is crucial and using a torque wrench helps achieve this. Equally important is the alignment. Ensure that the clamp sits perpendicular to the hose to avoid unnecessary strain and leaks. Installation is not just about where you place your clamp but how it’s placed—these small nuances often make a difference between a temporary fix and a long-lasting solution.
hose clamp 150mm
Applications and Use Cases
150mm hose clamps find considerable applications across industries. Whether it’s plumbing, automotive systems, or HVAC, their role in ensuring secure and leak-free connections cannot be overstated. In automotive applications, they ensure that coolant lines remain leak-free, maintaining engine temperature stability. In HVAC systems, they maintain airtight seals in duct connections, contributing to energy efficiency and effective climate control. Always consider the environment—temperature, pressure, chemical interactions—where the hose clamp will operate, as these will dictate the most suitable type and material.
Quality Assurance and Standards
Ensuring that your clamp adheres to industry standards is non-negotiable. ISO and BS standards are benchmarks for quality, offering assurance of reliability and safety. Investing in a clamp that adheres to these standards not only prolongs the lifespan of your system but also protects against potential liabilities. Manufacturers certified by these standards prioritize quality in production, ensuring that each component performs optimally.
Innovative Trends and Future Outlook
The landscape of hose clamps is not stagnant; new innovations and materials arise as industries evolve. Smart clamps equipped with sensors are on the horizon, offering real-time data on their state and effectiveness. Integrating IoT (Internet of Things) with traditional hardware like hose clamps is not far-fetched, promising even greater system monitoring and longevity.
In conclusion,
the humble 150mm hose clamp is an unsung hero in mechanical systems. With appropriate material selection, design understanding, and adherence to quality standards, you can enhance your systems’ reliability and performance. By staying informed about innovations, you ensure that your applications remain at the forefront of technology, driving both sustainability and operational success.