Heavy hose clamps play a fundamental role in various industries, ensuring a tight seal and secure connection between hoses and their fittings. These durable metal clamps are designed to withstand high pressure and adverse conditions, making them essential for applications in automotive, industrial, marine, and agricultural sectors. Understanding the multifaceted utility and importance of heavy hose clamps enriches our perspective on their role in modern engineering and mechanics.
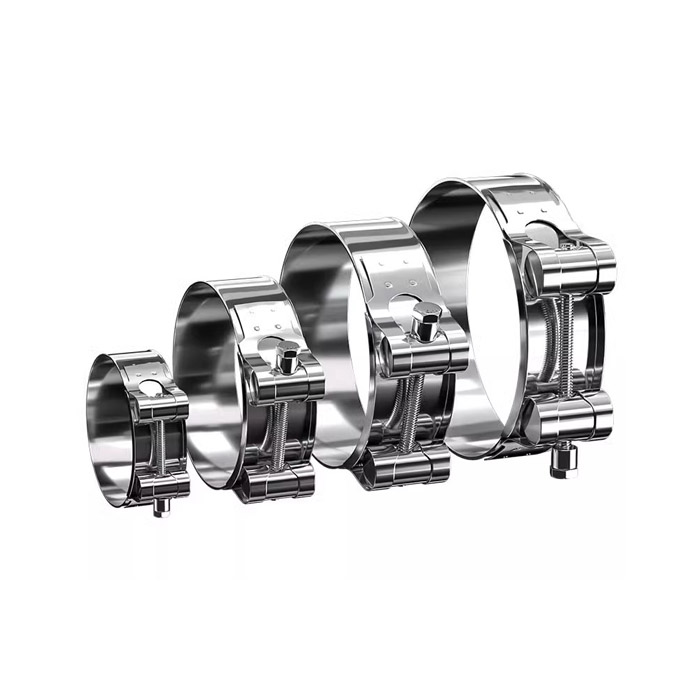
These clamps are often constructed from high-grade stainless steel or other robust metals, providing unmatched strength and corrosion resistance. Their design allows them to fasten hoses to fittings with a consistent and even pressure distribution, preventing leaks and ensuring operational efficiency. The choice of material is crucial; stainless steel variants offer the best protection against rust, especially in environmental conditions where moisture is prevalent, such as in marine or outdoor agricultural settings.
In the automotive industry, heavy hose clamps are indispensable. They secure coolant, fuel, and air hoses under the hood, ensuring that the vehicle operates smoothly and safely. Automotive systems rely on precision and reliability, and a malfunction due to a faulty clamp could lead to overheating or fuel leaks, compromising vehicle performance and safety. Therefore, automotive professionals often prefer heavy-duty clamps not only for their strength but also for their resilience to high temperatures and engine vibrations.
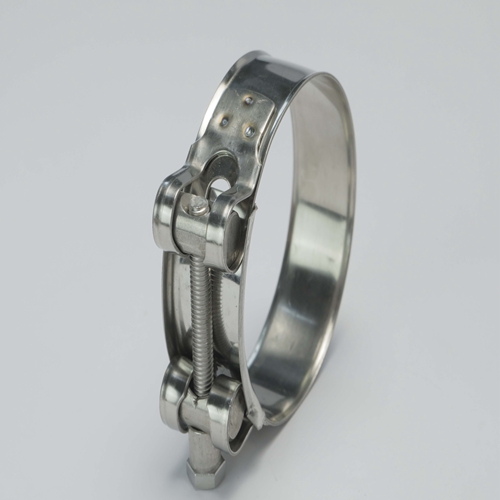
In industrial applications, the role of a heavy hose clamp is equally critical. Machines and production lines utilize numerous hoses to transport fluids and gases. In such high-stakes environments, a clamp’s failure could lead to costly downtime and extensive repairs. Heavy hose clamps provide peace of mind, maintaining the integrity of systems under extreme pressure conditions and ensuring continuous production flow.
For marine applications, the corrosive nature of saltwater presents a unique challenge. Heavy hose clamps must resist this corrosion to prevent failures in vital systems such as water and fuel lines. Stainless steel clamps are favored in these settings, but additional protective coatings and treatments can further extend their lifespan and reliability.
Agricultural machinery benefits greatly from the use of heavy hose clamps. Equipment such as tractors and irrigation systems depend on these clamps to maintain their fluid systems. Here, exposure to dirt, water, and mechanical stress underscores the necessity for a clamp that can withstand not only environmental factors but also the rigors of frequent use.
heavy hose clamp
Selecting the right heavy hose clamp for a specific application requires understanding several factors the size of the hose, the operating pressure, temperature ranges, and the environmental conditions. Mismatched sizes or incorrect materials can lead to system failures, risking safety and functional interruptions.
Installation technique also plays a vital role in a clamp’s effectiveness. Ensuring that clamps are not over-tightened prevents damage to hoses while ensuring they are held firmly in place. Regular inspections and maintenance are also recommended, as even the most durable clamps can degrade over time due to wear and environmental exposure.
Heavy hose clamps are backed by a wealth of expertise and research, with manufacturers constantly innovating to improve their design and materials. Companies involved in their production often collaborate with engineers and industry experts to refine clamp designs to meet the evolving demands of modern industrial applications.
Trust in heavy hose clamps is built over time. Industry professionals understand the critical role these components play and the importance of quality assurance in their performance. Reputable manufacturers provide detailed specification sheets, performance guarantees, and robust customer support, thereby establishing trustworthiness and authority in the market.
In conclusion, heavy hose clamps are pivotal to many mechanical systems, ensuring operational reliability and safety. By integrating expertise and innovation, they have become indispensable components across various sectors. Their continued evolution promises enhanced performance and durability, safeguarding the future of critical systems in diverse applications.