In the intricate world of mechanical applications, the precision and reliability of components can make or break performance outcomes. Among these critical components are flex hose clamps, which, despite their small size, play an indispensable role in ensuring the proper function and safety of various systems. They may seem like simple devices, but selecting the right flex hose clamp requires a depth of expertise and understanding of their function and design.
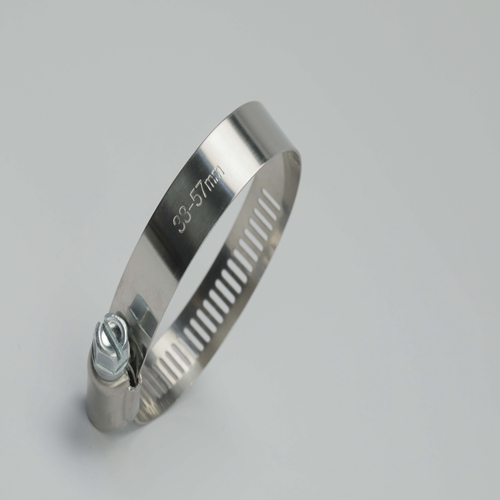
Flex hose clamps are engineered to secure flexible hoses onto fittings, preventing leaks of gases or liquids. Their design must accommodate a dynamic environment where pressure fluctuations, temperature changes, and physical movements are common. The expertise necessary to develop such clamps combines material science knowledge with mechanical engineering excellence.
The materials used in manufacturing flex hose clamps typically include stainless steel, galvanized steel, and high-quality plastics, which confer the necessary resistance to environmental factors such as corrosion, temperature extremes, and physical deformation.
The choice of material is crucial because it impacts the clamp’s durability and efficiency. Stainless steel, for example, is preferable in environments with high moisture levels due to its excellent resistance to rust and corrosion.
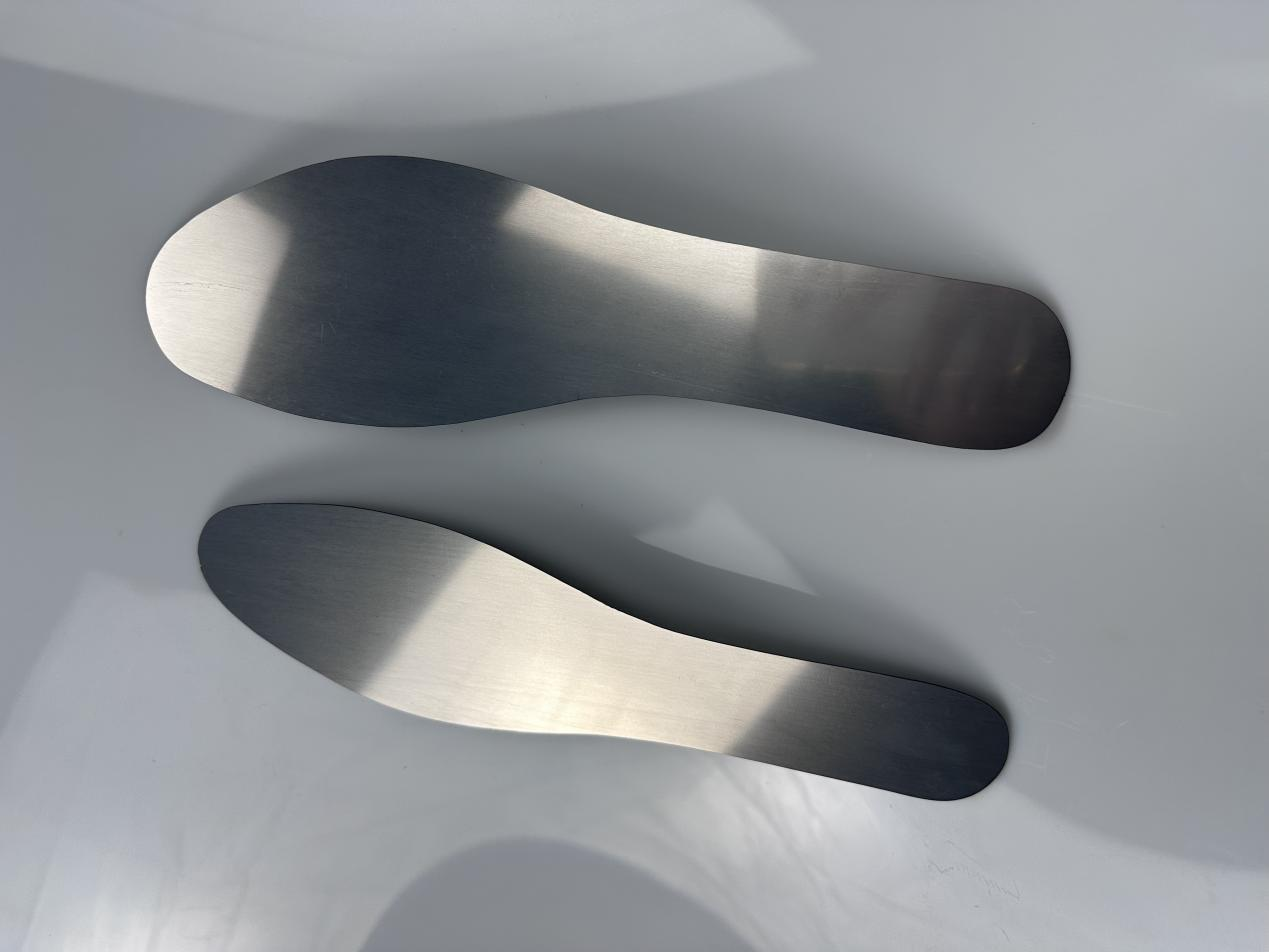
A key feature of the best flex hose clamps is their adjustability, which allows for a secure fit over hoses of various sizes while accommodating potential changes in the hose or the surrounding environment. This feature is particularly critical in industries where precision and adaptability are paramount, such as in automotive, aerospace, and HVAC systems. Here, the clamp's barb or worm drive mechanism ensures a tightly sealed connection that is also relatively easy to adjust when maintaining or replacing hoses.
flex hose clamps
The trustworthiness of a flex hose clamp is determined not just by its materials, but by the manufacturing process and quality control measures in place. Leading manufacturers employ stringent testing protocols, simulating real-world conditions to verify that each clamp can withstand expected stressors without failure. Consumers seeking reliability should prioritize products from companies with ISO certification or other third-party validations, which indicate adherence to rigorous standards.
When investing in flex hose clamps, it is vital to consider the clamp’s pressure rating and compatibility with your specific installation. Overlooking this could lead to catastrophic failure, resulting in costly system breakdowns or hazardous leaks. Consulting with professionals to match clamps with their intended applications is a best practice that optimizes system safety and efficiency.
Professional expertise in selecting flex hose clamps often involves an understanding of the latest technological advancements in this field. Advances such as enhanced coating technologies, which provide additional barriers against harsh chemicals or strengthened locking mechanisms, can be game-changers in highly specialized industries. Keeping abreast of such developments ensures that you leverage the most robust and cutting-edge solutions available.
In conclusion, the role of flex hose clamps in various mechanical systems cannot be overstated. Whether ensuring the smooth operation of a vehicle’s engine or maintaining the integrity of an industrial pipeline, their efficiency and reliability are crucial. An expert understanding of materials science, engineering principles, and the specific requirements of your application goes a long way in selecting the right clamp. For those committed to the highest standards of safety and performance, investing time in understanding these components and selecting the best available options is an essential undertaking.