Custom hose clamps have become indispensable tools across various industries, providing both versatility and durability. These clamps are specifically designed to secure hoses in place, preventing leaks and ensuring efficient fluid conveyance under challenging conditions.
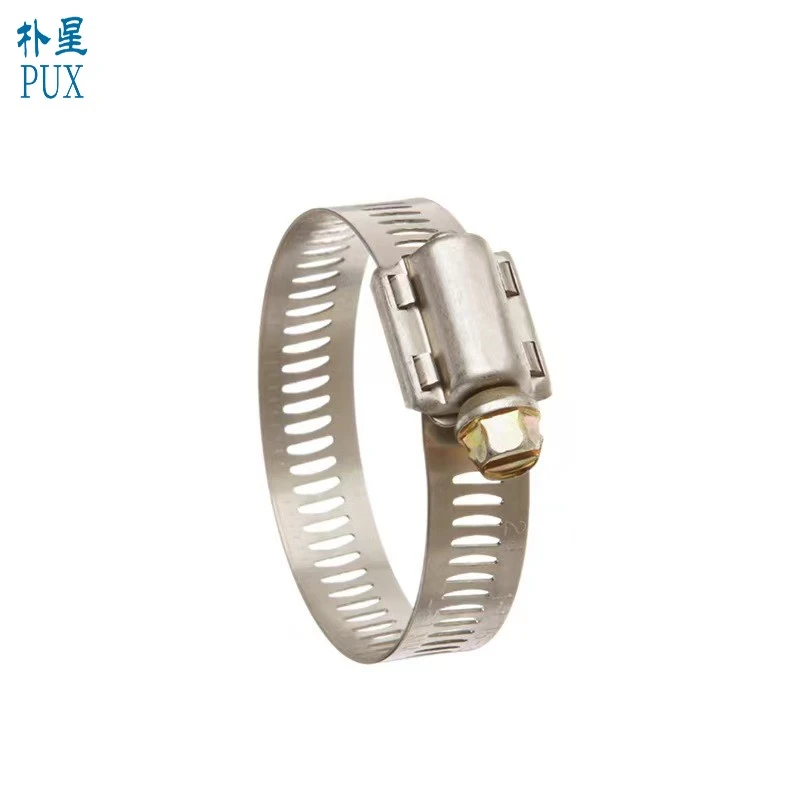
One of the primary advantages of custom hose clamps is their adaptability. Unlike standard clamps, which are designed for generic applications, custom clamps can be tailored to meet specific requirements. Industries such as automotive, aerospace, and manufacturing often deal with unique systems where standardized components fall short. Custom clamps can be manufactured to accommodate different hose diameters and pressures, thus ensuring seamless fits and superior performance.
Expertise in the design and manufacture of custom hose clamps involves a deep understanding of materials and engineering principles. Stainless steel remains a popular choice due to its resistance to corrosion and ability to endure fluctuating temperatures. However, for environments exposed to more corrosive substances or higher temperatures, specialized coatings and materials like thermoplastics or aluminum composites may be employed. This knowledge ensures that the right clamp is used for the right application, minimizing risks of failure.
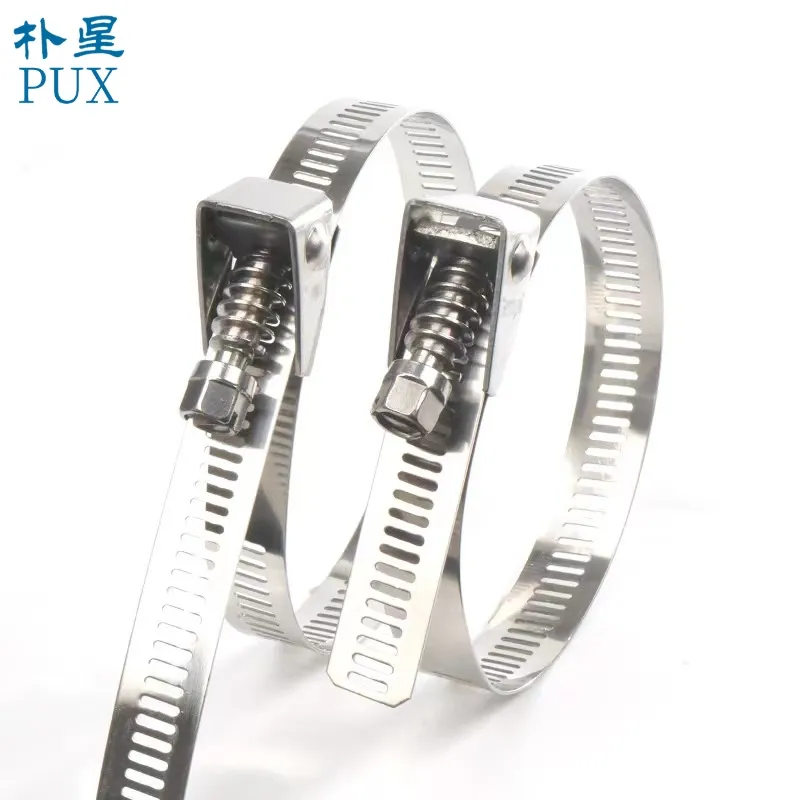
Real-world experience underscores the reliability of custom hose clamps. For instance, in the automotive industry, where engines and systems are becoming increasingly compact and efficient, custom clamps have emerged as essential components. Engineers routinely deal with squeezing more components into ever-tighter spaces while maintaining performance and ease of maintenance. Tailored clamps allow for innovative hose routing and secure connections, which standard clamps cannot achieve. This adaptability directly translates into better engine performance and lower maintenance overheads.
The construction industry also benefits significantly from custom hose clamps. Heavy machinery and equipment often have hydraulic systems that operate at extremely high pressures. Custom clamps in these scenarios are engineered to handle such stresses, ensuring that operations are smooth and downtimes are minimized. Feedback from field engineers and mechanics highlights that using sub-standard or incorrectly sized clamps can lead to catastrophic failures, highlighting the importance of proper customization.
custom hose clamps
When discussing authoritativeness and trustworthiness, it is imperative to rely on manufacturers and suppliers who have established themselves as leaders in the field of custom hose clamps. Companies offering these products often possess certifications such as ISO 9001, which guarantee that they adhere to stringent quality control standards. Moreover, many companies are also involved in industry boards and associations that set the benchmarks for hose clamp manufacturing, further enhancing their credibility.
Another crucial aspect is the consultation process involved in acquiring custom hose clamps. Trustworthy suppliers often have technical experts who work alongside clients to understand the specific needs of their systems. They offer guidance on material selection, corrosion resistance, and load capacity, ensuring that the final product meets both performance expectations and safety standards. Such collaboration not only builds trust but also fosters long-term partnerships.
Furthermore,
investing in custom clamps can be economically prudent. Although the initial costs might be higher than purchasing off-the-shelf components, the long-term benefits of reduced maintenance, fewer replacements, and improved system efficiency often far outweigh the initial expense. Real-world case studies often highlight companies experiencing significant savings over time through the use of custom solutions.
In summary, custom hose clamps are more than just components; they are critical to the reliability and efficiency of complex systems. Their adaptability, combined with expert design and manufacture, makes them suitable for a variety of demanding applications. Through careful selection and collaboration with trusted suppliers, companies can ensure that their systems perform optimally and stand the test of time. Employing custom solutions reflects a commitment to quality, safety, and efficiency, qualities that are paramount in any industry.