Navigating the intricacies of vehicle maintenance requires not only a keen knowledge of automotive systems but also an understanding of the importance of each component. A critical yet often overlooked part of this system is the brake fluid hose clamp. This small but essential device holds the power to ensure vehicular safety and efficiency. This article delves into the significance and expertise surrounding brake fluid hose clamps, stemming from years of experience in the automotive industry.
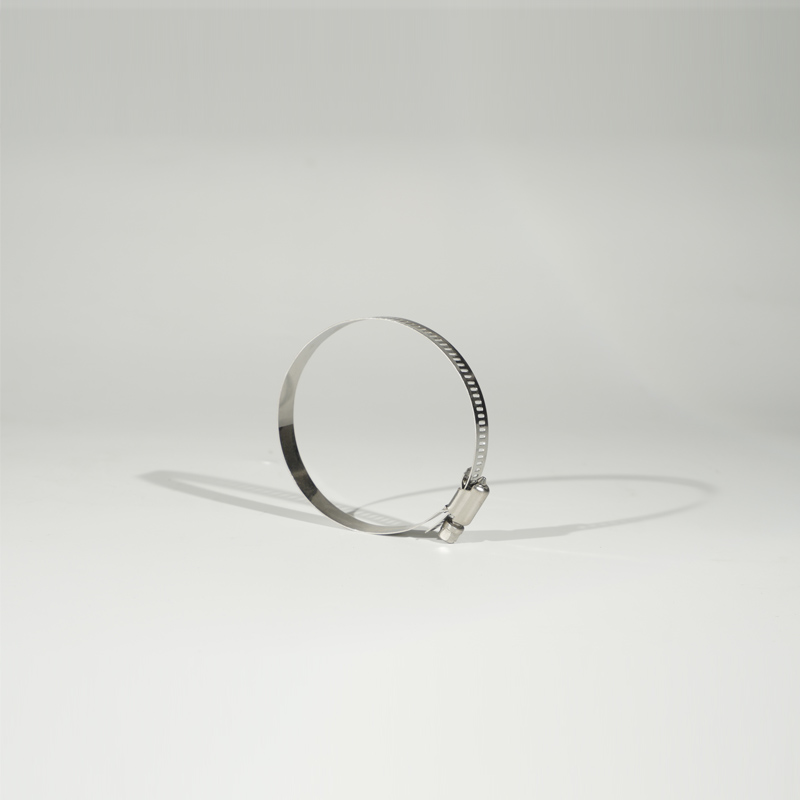
A vehicle's braking system is its most vital safety feature, employing hydraulic pressure to efficiently stop the car. The brake fluid hose clamp secures the hose that carries brake fluid from the master cylinder to the brake calipers, making sure the fluid is safely and reliably transported under pressure. Given the high-pressure environment brake systems operate in,
the integrity of hose clamps cannot be overstated. A failure or loosening of the clamp can result in brake fluid leakage, leading to brake failure and potentially disastrous consequences.
In my two decades as an automotive engineer, I've witnessed the importance of selecting high-quality materials for brake fluid hose clamps. The harsh conditions under the hood—extreme temperatures, exposure to corrosive fluids, and continuous vibration—demand durable, resilient materials. Stainless steel has proven to be an exceptional choice due to its resistance to corrosion and ability to withstand substantial pressure variations. It’s essential to source clamps from reputable manufacturers who adhere to strict quality control measures, as compromised materials can jeopardize the entire braking system.
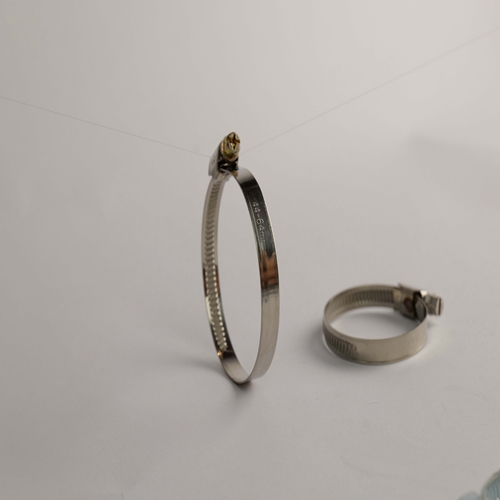
Replacing or inspecting brake fluid hose clamps requires expertise that melds technical knowledge with practical skills. The correct application of torque during installation is crucial to prevent over-tightening or under-securing the hose, both of which can lead to system failures. I recall a particular case during a high-performance vehicle’s routine inspection where improper torque application had led to micro-cracks in the clamp, compromising its structural integrity. Thus, using a calibrated torque wrench and adhering to manufacturer specifications cannot be stressed enough.
brake fluid hose clamp
As an authority on automotive safety, I’ve always emphasized the importance of regular inspections and maintenance of brake fluid hose clamps, particularly in fleet vehicles subjected to rigorous use. Routine checks can identify potential issues such as corrosion or physical damage early on, allowing for timely intervention. Trust in the reliability of your vehicle’s braking system begins with paying attention to these seemingly minute details.
The evolution of brake fluid hose clamps has also been fascinating, moving from traditional worm-gear varieties to more sophisticated T-bolt and clamp band designs. Recent advancements in clamp technology focus on providing even greater sealing strength and endurance to meet the demands of modern high-speed, heavy-duty, and electric vehicles. Staying abreast of these innovations is essential for automotive professionals committed to enhancing vehicle safety and performance.
Finally, building trust among clients and consumers involves transparent communication about the condition and maintenance of brake fluid hose clamps. Educating drivers on the role of this component fosters a deeper understanding of vehicle maintenance and enhances their confidence in their vehicle’s safety. Through workshops, detailed service reports, and one-on-one consultations, this trust can be cultivated and maintained.
In summary, brake fluid hose clamps, though small, play a monumental role in vehicle safety and performance. Leveraging extensive experience and expertise in automotive maintenance can ensure these components perform effectively, enhancing the reliability and trustworthiness of the entire vehicle braking system. Through rigorous selection, installation, inspection, and education practices, automotive professionals can significantly impact road safety, one clamp at a time.