When it comes to securing hoses in a myriad of applications, the 7/16 hose clamp is a small yet crucial component that often goes unnoticed until needed. These clamps serve a wide array of purposes across industries, from automotive to plumbing, and even in aerospace applications. Understanding the nuances of these versatile devices is essential for professionals and DIY enthusiasts alike, ensuring not only efficiency but also safety in operations.
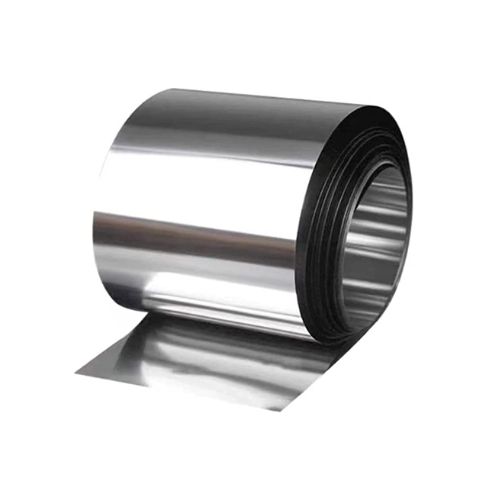
Expertise plays a key role in the proper application and selection of 7/16 hose clamps. These clamps are typically made from durable materials such as stainless steel or galvanized steel, each offering unique advantages. Stainless steel is particularly chosen for its superior resistance to corrosion and rust, making it ideal for use in environments exposed to moisture or chemicals. Meanwhile, galvanized steel provides a cost-effective solution with adequate protection for less demanding environments.
To harness the full potential of a 7/16 hose clamp, one must understand its construction. It typically comprises a metal band with a screw mechanism that, when tightened, exerts pressure around the hose. The precision in this mechanism ensures a secure attachment to the fitting while preventing leaks. Skilled professionals recognize the importance of not over-tightening these clamps, as excessive pressure could lead to the hose material weakening and eventually failing.
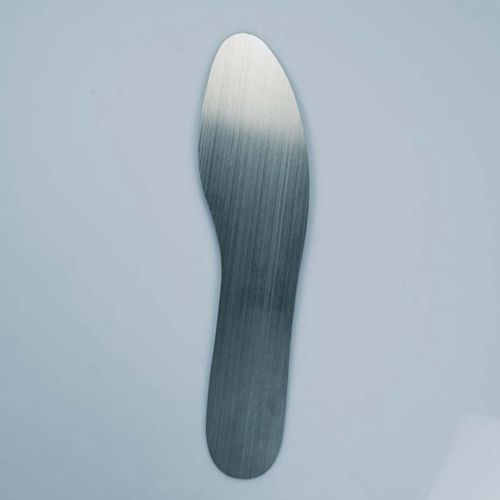
Authoritativeness in discussing 7/16 hose clamps comes from empirical studies and standardized testing. Industry standards, such as those from the American Society for Testing and Materials (ASTM), outline the performance requisites for these clamps. This includes factors like the torque capacity and the clamp’s ability to maintain a seal under pressure variations. For critical applications, relying on clamps that meet or exceed such standards is non-negotiable, as failure could result in catastrophic consequences.
7/16 hose clamp
Real-world experience further solidifies trustworthiness when handling hose clamps. In automotive applications, for instance, mechanics frequently employ 7/16 hose clamps to secure fuel lines or coolant hoses. Here, the ability to maintain a robust seal despite the vibrations and thermal fluctuations encountered during engine operations is a testament to the clamp's reliability. Another example is in the field of marine applications, where the clamps must withstand not only corrosion but also the constant flexing caused by wave motion.
Trustworthiness also stems from consumer testimonials and brand reputation. Renowned manufacturers of hose clamps rigorously test their products, often providing warranties as a testament to their confidence in performance. Users consistently favor these products for their reliability and longevity, further backed by endorsements from industry experts who prioritize performance over cost.
In conclusion, the 7/16 hose clamp might seem insignificant at first glance, but it serves as a critical component across numerous applications. Its effectiveness hinges on a comprehensive understanding of material properties, mechanical construction, and industry standards. By appreciating these facets, users can ensure optimal performance and safety. Additionally, selecting products from reputable manufacturers, whose commitment to quality is backed by industry certifications and positive consumer feedback, further instills confidence in their application. Emphasizing these attributes will not only enhance one's application outcomes but also uphold the integrity and reliability expected in high-stakes environments.