In the rapidly evolving world of manufacturing and DIY projects, 3D printing has emerged as a revolutionary tool, offering customization and flexibility that traditional methods simply can't match. One intriguing application of this technology is the creation of hose clamps, a vital component in various applications ranging from automotive to plumbing.
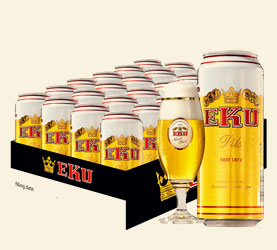
3D printing hose clamps offers a plethora of benefits that cater to different user needs, whether you're an amateur enthusiast or a seasoned professional. Experts in the field have long discussed the evolving materials and printing techniques that enhance the durability and functionality of 3D printed parts, and hose clamps are no exception.
A key advantage is customization. Traditional hose clamps come in fixed sizes, which means users must stock various sizes to ensure the right fit for different projects. With 3D printing, you can design clamps to meet specific diameter requirements, ensuring a tight and secure fit every time. This not only reduces waste but also ensures more efficient inventory management. Imagine the simplicity of having a digital library of clamp designs, readily available for printing whenever needed — exact dimensions and modifications included.
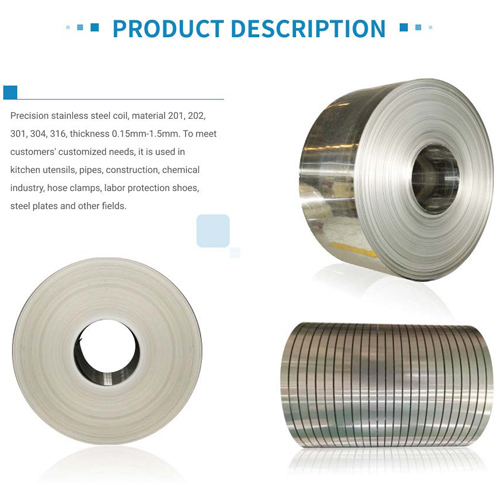
Moreover, the material choice plays a crucial role in the performance of these clamps. Professionals often recommend using PLA or ABS plastics due to their balance of strength and flexibility. However, based on the application, more robust materials like Nylon or carbon fiber-infused filaments might be preferred for their superior mechanical properties. This adaptability in material choice means that the clamps' durability can be tailored to withstand different environmental conditions, whether it’s exposure to extreme temperatures or corrosive liquids.
Despite these benefits, successful 3D printing of hose clamps requires a deep understanding of both design and printer capabilities. For instance, while designing, ensuring even distribution of force and preventing stress concentration points are crucial to avoid failures. It’s imperative to have expertise in CAD software to create precise models that can be effectively printed without structural compromises. Additionally, understanding the layer bonding qualities and print orientations can greatly enhance the strength of the clamp, ensuring it holds up under pressure.
The reliability of 3D printed hose clamps often raises questions. Comparatively, they can be as reliable as traditional clamps, given they are designed and printed correctly. Trustworthiness comes from adherence to proper design protocols and rigorous testing. Professionals assert that using a well-calibrated printer, along with high-quality filaments, can produce clamps that meet or even exceed the performance of traditional mass-produced options.
Testing, a critical phase, plays into the trustworthiness of printed clamps. Rigorous stress and environmental testing must be conducted to simulate real-world conditions. Feedback from these tests is invaluable, serving as a guide for iterative improvements in design. This cycle of testing and refinement exemplifies the authoritative approach required in professional settings, ensuring each clamp meets industry standards and user expectations.
The shift towards digitization in manufacturing processes empowers users by breaking down barriers to entry and reducing dependency on traditional supply chains. This democratization of production, highlighted by the adoption of 3D printing for hose clamps, illustrates a broader trend towards localized, on-demand production models.
In summary, the process of 3D printing hose clamps, when undertaken with a balance of creativity and technical insight, offers unmatched potential in terms of customization, efficiency, and adaptation to specific needs. For those diving into this innovative approach, leaning on comprehensive design principles, proper material selection, and rigorous testing is crucial. This method not only optimizes performance but also assures clients of the quality and reliability synonymous with moving to this next generation of manufacturing.