The often-overlooked hose clamp plays a crucial role in ensuring the efficiency and safety of numerous mechanical systems. Known for their utility in securing hoses over fittings, hose clamps are indispensable in industries ranging from automotive to plumbing and even aviation. To the unassuming eye, these small devices might seem simple, yet choosing the right hose clamp requires understanding its types, applications, and the specific requirements of the task at hand.
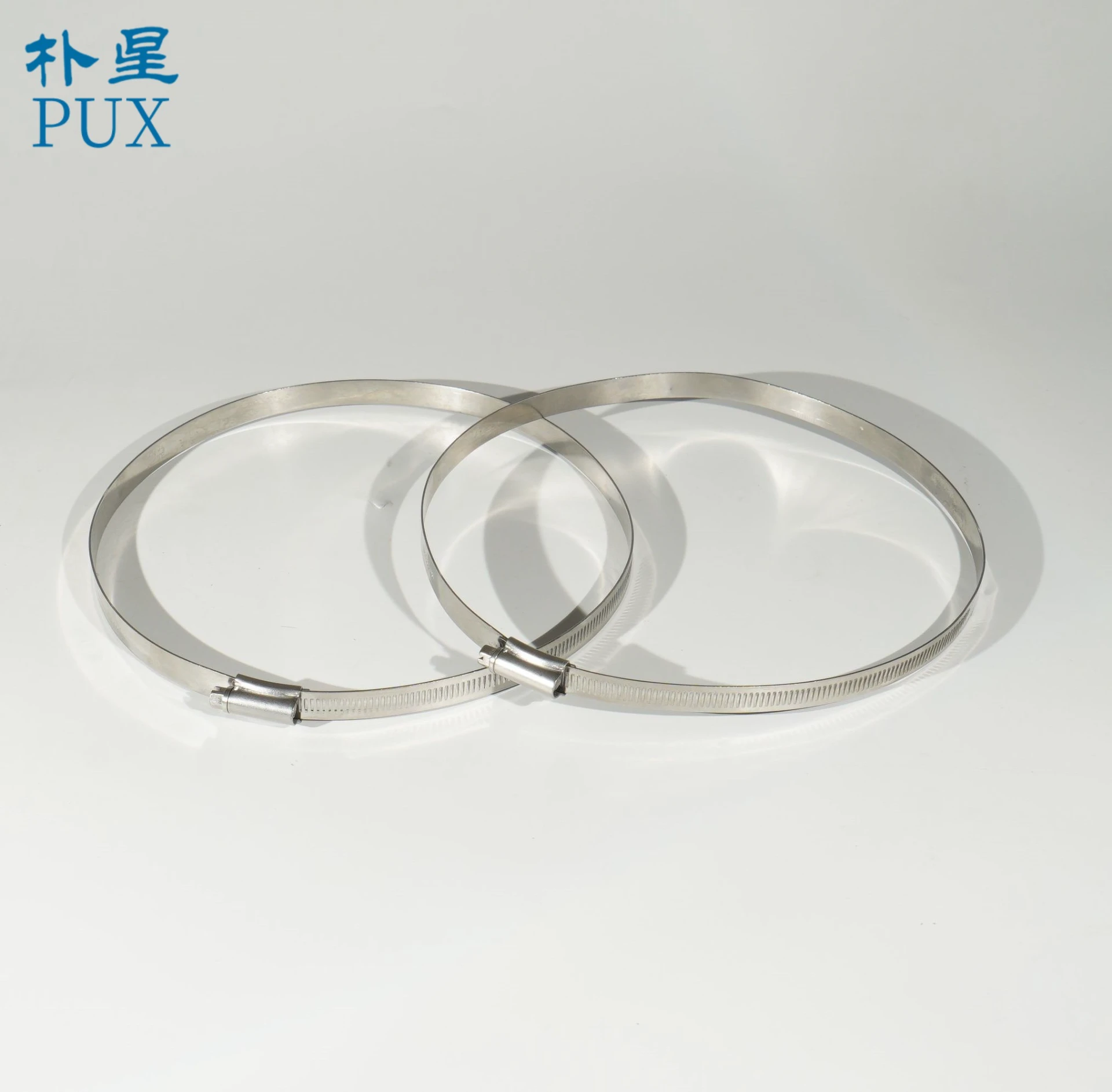
Hose clamps are available in various designs, each uniquely suited for particular tasks. The most prevalent types include worm-drive, spring,
and wire clamps. Worm-drive hose clamps are favored for their adjustability and strong grip, ideal for automotive applications where hoses may expand and contract under varying temperatures and pressures. Spring clamps, on the other hand, are self-tightening and can accommodate fluctuations in hose diameter, making them valuable in HVAC systems and in scenarios where rapid installation is critical. Wire clamps are more rudimentary but are nonetheless effective in low-pressure applications, including household plumbing.
Selecting a hose clamp that meets both the mechanical demands and environmental conditions of your application is paramount. For instance, in the automotive industry, clamps must withstand exposure to motor oil, coolant, and brake fluid. Stainless steel worm-drive hose clamps often emerge as the optimal choice here due to their resilience against corrosion and temperature extremes. In contrast, for household plumbing requirements, a nylon clamp might suffice—especially for temporary solutions—due to its cost-effectiveness and satisfactory performance in less demanding conditions.
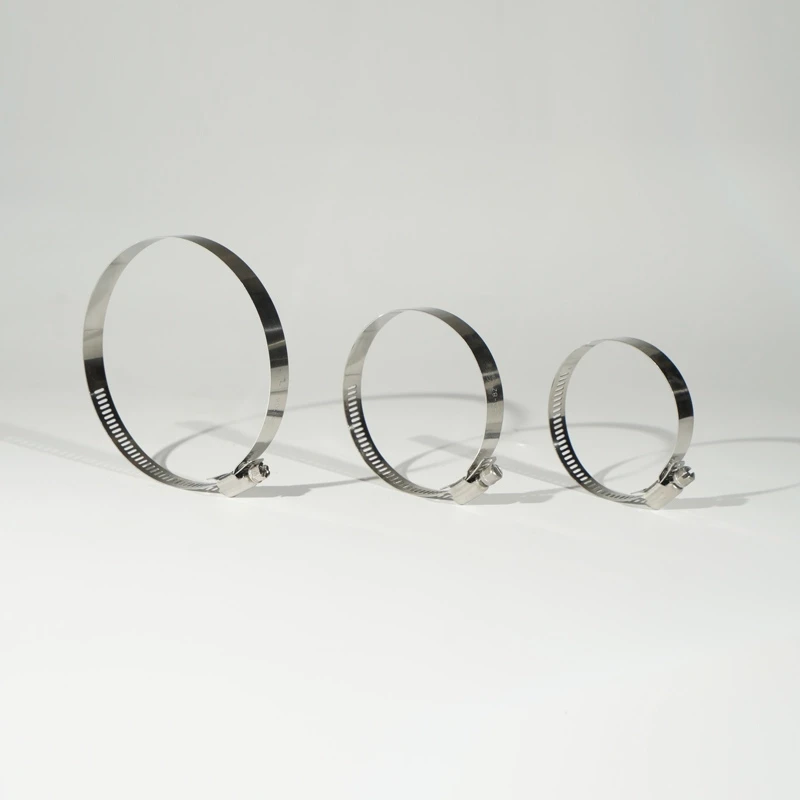
Expertise knowledge suggests that improper selection and installation of hose clamps can lead to catastrophic failures. A loose clamp in an automobile could result in coolant leaks, leading to engine overheating, while a corroded clamp in a marine environment could fail, causing potentially serious safety hazards. Moreover, over-tightening can damage hoses, leading to cracks and consequent leaks. Therefore, the correct technique—tightening the clamp to the manufacturer’s recommended torque specifications—is crucial.
hose clamps
From an authoritative perspective, consulting industry standards and trusted brands enhances reliability and safety. Manufacturers that rigorously test their clamps, such as Norma Group or Oetiker, ensure their products can withstand high pressures and variable environmental conditions. Referring to industry standards, such as SAE (Society of Automotive Engineers) guidelines, assures that the clamps chosen meet essential safety requisites.
To instill trust among users, transparency regarding a hose clamp’s capabilities is non-negotiable. Providing detailed product information, including material composition, size range, and maximum pressure capacity, builds confidence. Additionally, offering insights into common failures and preventive maintenance extends the lifespan of both the clamp and the overall system it supports, ensuring a reduction in unforeseen breakdowns.
Knowledge gain from real-world experience amplifies product improvement and user satisfaction. Listening to feedback from technicians and end-users helps identify weaknesses in current designs that might require innovation. Incorporating this data can lead to the development of more durable, easier-to-use clamps that accommodate the ever-evolving needs of modern industry.
In summary, the significance of selecting the correct hose clamp cannot be overstated. It involves assessing the task requirements, understanding the environmental conditions, relying on well-tested products, and educating users about proper installation techniques. Through a commitment to quality, transparency, and constant improvement, the humble hose clamp continues to uphold its status as an unsung hero in various industries.