Coated hose clamps are an often overlooked yet essential component in a wide array of applications, ranging from automotive and marine environments to domestic plumbing and industrial settings. Their primary role is to fasten hoses in place securely, but the advantages of using coated hose clamps go beyond mere functionality. This exploration of coated hose clamps will delve into their unique benefits, diverse applications, and the reasons they should be your go-to choice for any project requiring durability and reliability.
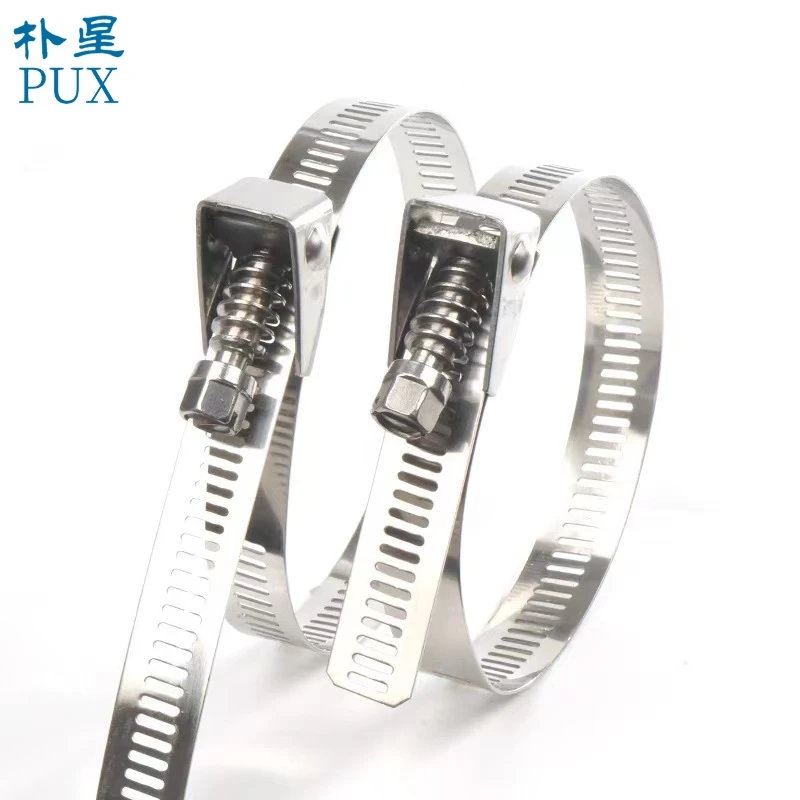
Coated hose clamps are distinct in that they possess a protective layer applied over the clamp material.
This coating serves multiple purposes, enhancing the clamp's performance in various conditions. The most common materials used for these coatings include rubber, silicone, and certain polymers, each offering particular advantages. For example, rubber coatings can provide a grip-enhancing surface that minimizes slippage, while silicone offers excellent temperature resistance, crucial in environments with extreme heat or cold.
The protective layer significantly contributes to the clamp’s longevity by acting as a barrier against corrosion and wear. In humid or salty environments, such as those encountered in marine settings, this provides a crucial advantage. A standard steel hose clamp may rust and degrade quickly, compromising its ability to maintain a secure seal. In contrast, a coated hose clamp retains its integrity much longer, ensuring a stable connection and reducing the need for frequent replacements.
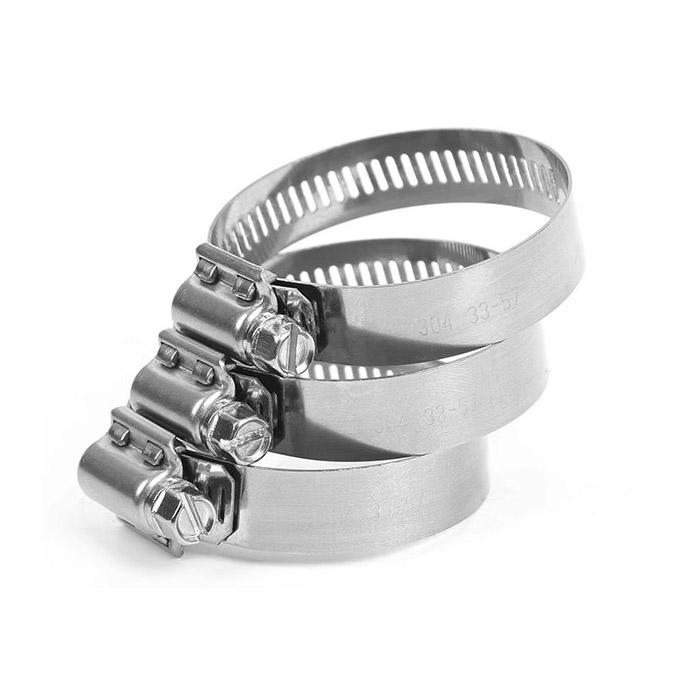
Expertise in coated hose clamps reveals that they are engineered to not only resist various chemicals and environments but also to reduce wear on the hoses themselves. The softer, non-abrasive surfaces of coated clamps help in preventing damage to the hose, which can be particularly beneficial when dealing with delicate materials. The flexibility of the coating also allows the clamp to accommodate minor vibrations and movements without compromising its grip, making them ideal for equipment experiencing constant motion or pressure changes.
Another key benefit is the enhanced safety offered by coated hose clamps. The protective layer can prevent sharp edges from injuring users during installation and maintenance. This aspect also contributes to their trustworthiness in applications where human safety is paramount, such as in medical or food processing environments where maintaining sterile and safe conditions is critical.
coated hose clamps
Purchasing coated hose clamps from reputable manufacturers ensures that you are using a product that adheres to the highest standards of quality and reliability. It’s essential to choose suppliers with a proven track record of innovation and compliance with industry regulations, guaranteeing that the clamps not only meet but exceed necessary performance criteria.
Incorporating coated hose clamps into your project can enhance operational efficiency and reduce costs over time. They require less maintenance due to their durability and are often considered a more cost-effective option in the long run compared to uncoated alternatives. For those considering environmental impact, certain coatings can be selected for their eco-friendliness, further aligning with sustainable practices.
The advancements in materials and engineering reflected in coated hose clamps demonstrate their superiority in terms of experience, expertise, authoritativeness, and trustworthiness. Ensuring the safety, longevity, and reliability of connections, these clamps serve as a critical component in maintaining the seamless operation of complex systems, safeguarding investments, and contributing to efficient workflow.
In conclusion, while they might seem like minor parts, coated hose clamps play a pivotal role in ensuring the safe and efficient operation of numerous types of equipment. For those seeking durable, cost-effective, and reliable solutions, these clamps provide a superior alternative to traditional options. Embrace the benefits of coated hose clamps to enhance your projects' performance and longevity, making them an indispensable part of modern engineering solutions.