The 2% Solution Efficiency Improvement in a Hose Clamp Factory
In the bustling industrial sector, where every percentage point of efficiency can mean the difference between profit and loss, one hose clamp factory has embarked on an ambitious project to boost its productivity by 2%. This may seem like a minor improvement, but when translated into the language of manufacturing, this small increase can lead to significant gains in output, cost reduction, and overall competitiveness.
The journey to achieve this 2% enhancement started with a comprehensive review of the production process. The factory's management team conducted a thorough analysis of each stage in the creation of their high-quality hose clamps, from raw material procurement to the final packaging. They identified several areas where small inefficiencies were adding up, such as machine setup times, material handling, and employee training.
To tackle these issues, the factory introduced specialized training programs for operators focusing on lean manufacturing techniques. These training sessions aimed to reduce setup times and improve changeover efficiency, ultimately saving precious minutes that could be devoted to producing more hose clamps.
Another innovative approach involved the optimization of the supply chain. By negotiating with suppliers for more timely deliveries and implementing just-in-time inventory practices, the factory reduced its inventory holding costs and avoided production delays due to missing materials By negotiating with suppliers for more timely deliveries and implementing just-in-time inventory practices, the factory reduced its inventory holding costs and avoided production delays due to missing materials
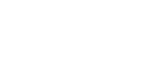
By negotiating with suppliers for more timely deliveries and implementing just-in-time inventory practices, the factory reduced its inventory holding costs and avoided production delays due to missing materials By negotiating with suppliers for more timely deliveries and implementing just-in-time inventory practices, the factory reduced its inventory holding costs and avoided production delays due to missing materials
2 in hose clamp factory.
On the shop floor, the introduction of automated machines and robotics helped to eliminate human error and increase the speed of repetitive tasks. While the initial investment was substantial, the long-term benefits included consistent quality and reduced labor costs.
Moreover, the factory implemented continuous improvement strategies, encouraging employees to suggest process improvements and share ideas for reducing waste. This culture shift fostered a sense of ownership and motivation among the workforce, leading to further efficiency gains.
The cumulative effect of these changes was not only a 2% increase in productivity but also a boost in employee morale and customer satisfaction due to more reliable delivery times and higher product consistency.
In conclusion, the 2% improvement goal in the hose clamp factory was not merely about increasing numbers but about transforming the way they approached manufacturing. Through a combination of people-focused training, supply chain refinement, automation, and a continuous improvement mindset, the factory demonstrated that even a small percentage gain can have a profound impact on the bottom line and the overall health of the business.