In the realm of mechanical fasteners, hose clamps often don’t receive the recognition they deserve. Yet, these small components play a pivotal role in countless applications across diverse industries. Their job? To ensure secure connections that manage the flow of liquids and gases, effectively preventing leaks and maintaining system integrity. However, beyond their apparent simplicity lies a wealth of experience, expertise, and authoritative insights crucial for selecting the right hose clamp for your needs.
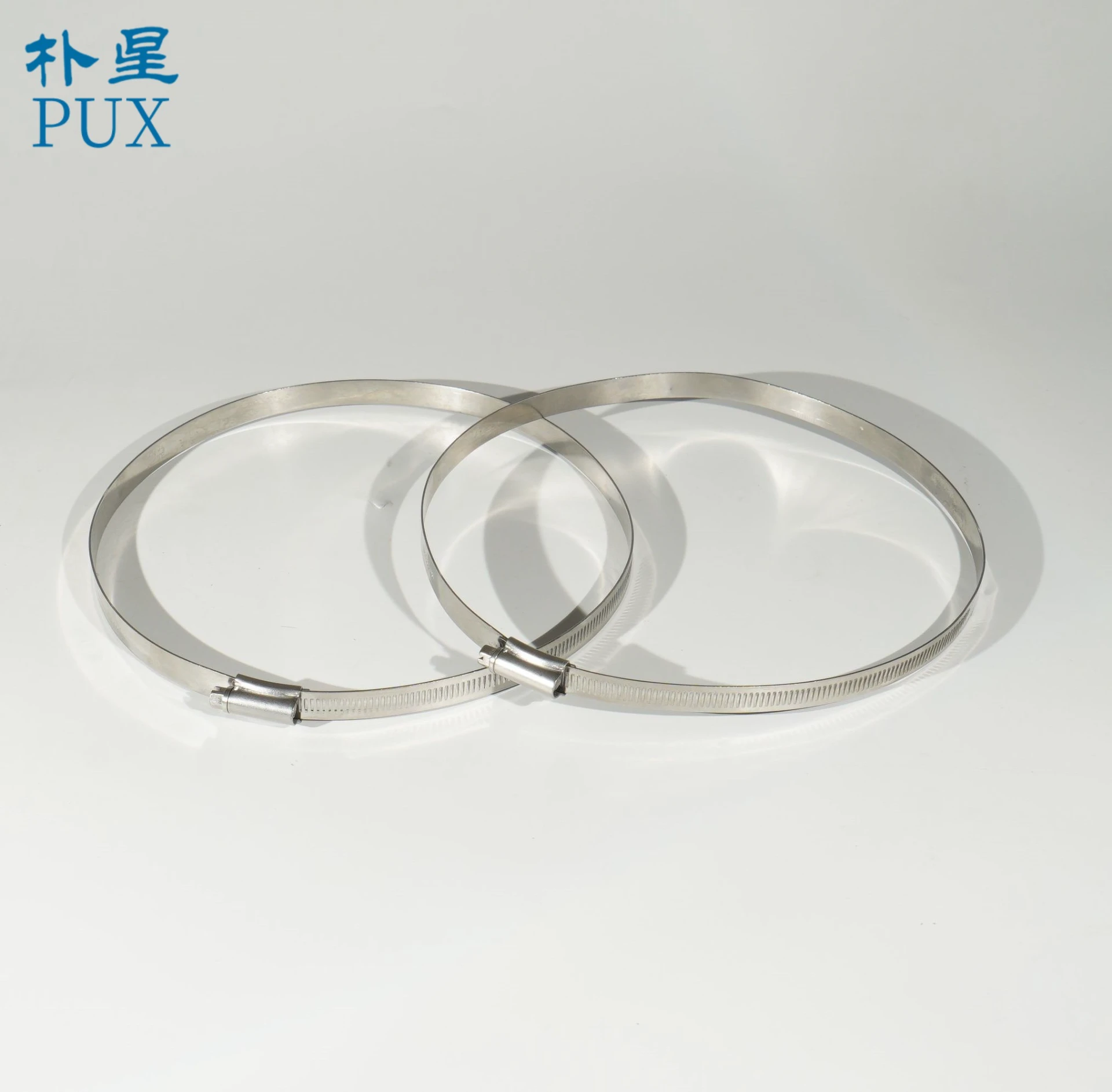
Material selection stands at the forefront of effective hose clamp application.
Understanding the environmental conditions your clamp will encounter is vital. For instance, stainless steel hose clamps provide exceptional corrosion resistance, ideal for marine applications where saltwater poses a significant threat. On the other hand, carbon steel clamps might be more suitable for dry, indoor environments due to their cost-effectiveness. Trusting a material without considering its suitability for your specific conditions can lead to premature failure and costly downtimes.
The type of hose clamp is another critical consideration derived from both expertise and empirical field experience. While screw and band clamps are prevalent, spring clamps offer the advantage of accommodating changes in pressure and temperature, making them suitable for applications in vehicle engines where thermal expansion is a concern. Conversely, click clamps, though less adjustable, provide robust security in systems where vibrations could lead to gradual loosening. It’s about matching the clamp’s design benefits to your operational needs—a decision that calls for both product knowledge and real-world application insight.
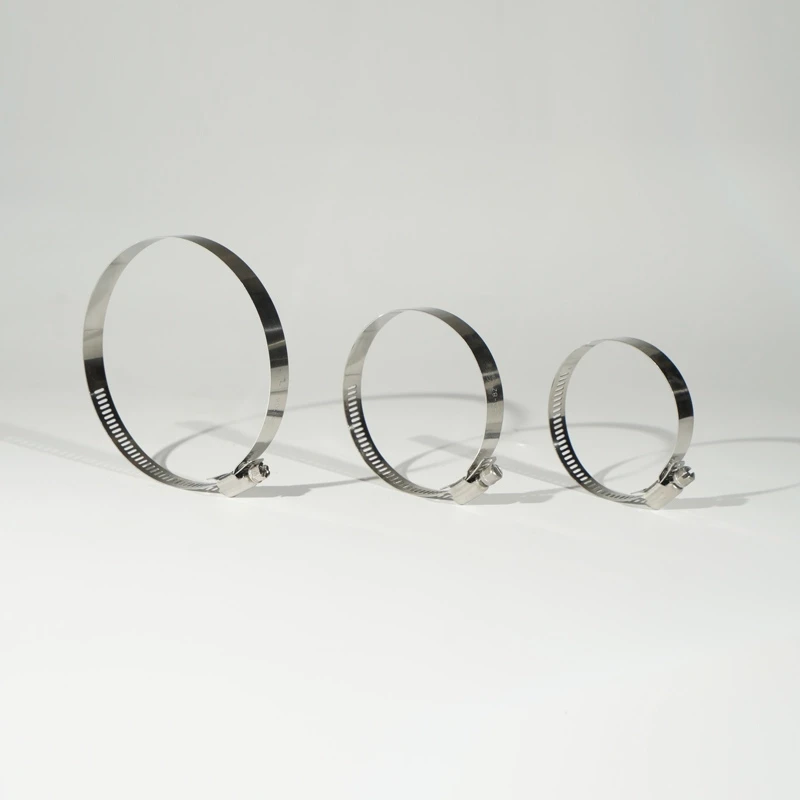
hose clamps
Moreover, installation techniques often underscore the authority of hose clamps. Tightening a clamp might seem straightforward, yet it requires a balance of force to ensure a secure fit without damaging the hose material. Over-tightening can cause cracks and leaks, while under-tightening may lead to detachment under pressure. Professionals advocate for torque specifications provided by manufacturers as a trustworthy guideline, promoting both the longevity of the clamp and the integrity of the connection. This authoritative approach ensures that installations adhere to best practices, aligning with manufacturer-designed performance standards.
Finally, ongoing maintenance and inspection should not be overlooked as they affirm both trust and authority in hose clamp applications. Routine checks for signs of wear, corrosion, or loosening can preemptively identify issues before they escalate into critical failures. In high-stakes applications, such as chemical processing or aviation, this maintenance is not merely a recommendation but a necessity, underscoring the clamp’s role as a reliable component in the overall system architecture.
In conclusion, the world of hose clamps is one steeped in subtle complexities that demand a blend of empirical knowledge, specialized expertise, and unwavering trust in proven methods and materials. By prioritizing these elements, one can ensure their systems operate efficiently, safely, and with a reduced risk of unexpected failures. Hose clamps may indeed be small, but their impact on operational success is immeasurable. Making informed, authoritative choices in their selection and application continues to be crucial for any industry wishing to maintain the highest standards of efficiency and reliability.